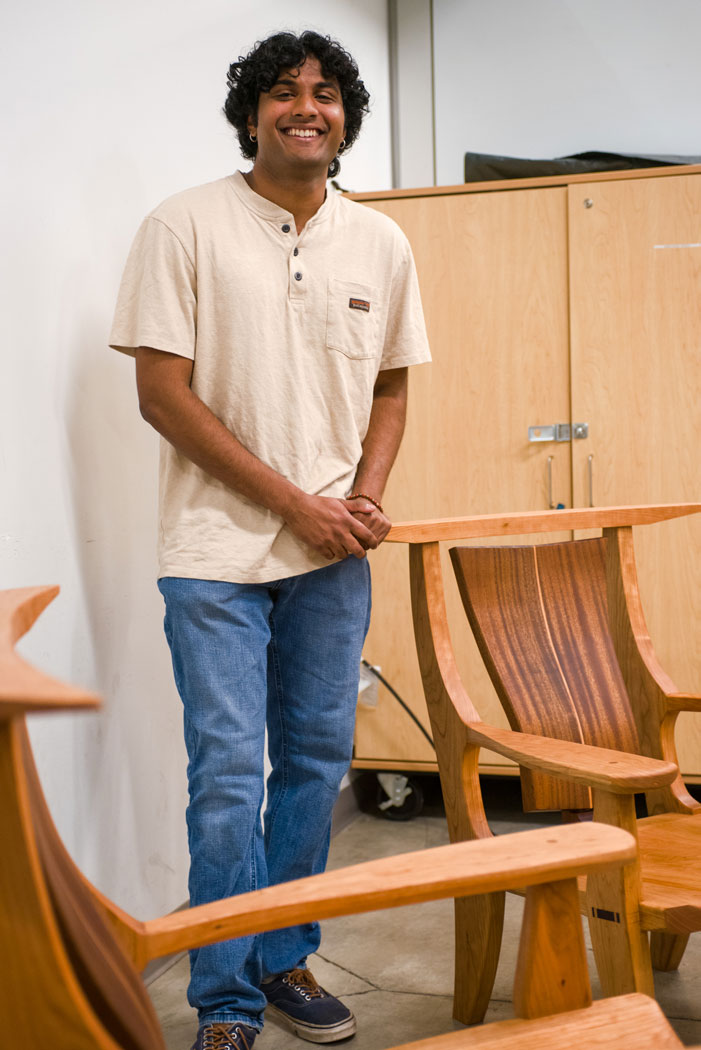
Photo by Mathew Burciaga
Fourth-year UC Berkeley student Mayuresh Visswanathan has found a way to channel his affinity for the natural world through a specific hobby: woodworking.
Over the last four years, Mayuresh has tapped into his creativity and an array of hand and power tools to build custom furniture. He recently participated in the Jacobs Institute for Design Innovation’s Winter 2023 showcase, displaying a pair of lounge chairs built at the makerspace in Jacobs Hall.
We spoke to Mayuresh about woodworking, furniture making, and his time at UC Berkeley.
This conversation has been edited for length and clarity.
What drew you to UC Berkeley, and toward majoring in both Forestry and Business Administration?
I grew up with a keen interest in the natural world and wanted to learn more about creating ecosystems where plants can thrive. I had no idea what forestry was before applying to Berkeley, but now I’ve learned that a large part of the field boils down to creating systems and conditions where a forest can thrive. Only then can it provide environmental and social benefits.
I’m also passionate about entrepreneurship and I wanted a Haas degree to learn more about business fundamentals. Cal seemed to be the ideal option for school, considering that it has the best business school and forestry program on the West Coast.
What were some highlights of the forestry program for you?
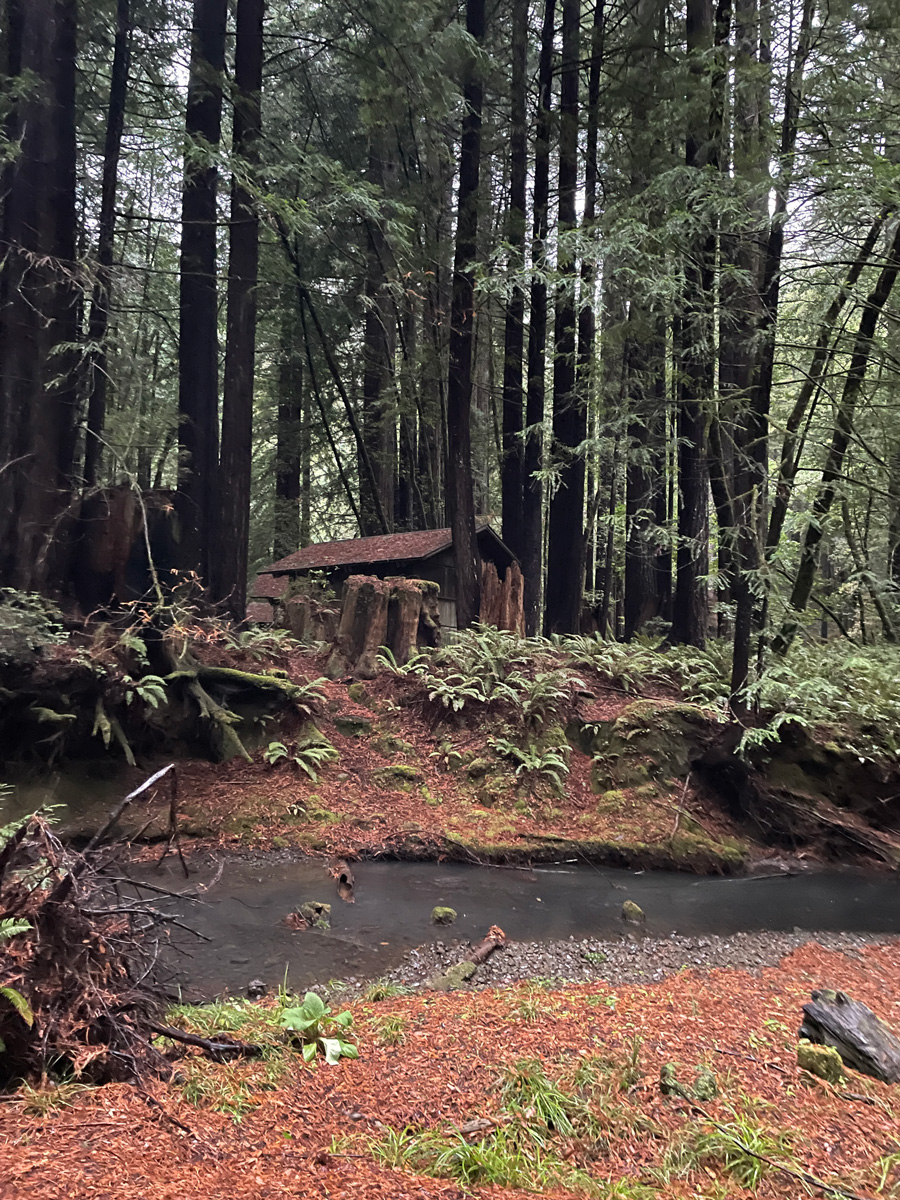
Photo by Mayuresh Visswanathan
My forestry classes have been incredible and offer opportunities for hands-on learning—something I’ve found to be rare at Berkeley. ESPM 134, ESPM 185, and ESPM 186 were among my favorites because we went on multiple field trips, including a few overnight trips. We got a firsthand look at the ecosystems we were learning about and were able to ask experts about real management challenges they face.
I also participated in the Forestry Field Camp in the Sierra Nevada, which was an amazing experience. Sampling macroinvertebrate populations and fish populations on stream ecology day was a highlight of camp. It was absolutely stunning—not only to see different creatures up close in the streams, but to also see the stretches of crystal clear water and little jungles of aquatic plants underwater.
Did you get involved in other research through Rausser College?
I got involved as a student researcher at the CRC after taking ESPM 72, a class on Geographic Information Systems (GIS), with Cooperative Extension professor Van Butsic. I was a first-year at the time and asked Van, who was then the CRC’s co-director, if there was an opportunity to work for the Center that summer. He was very receptive and offered me a position. I worked on a project that studied the distribution of licensed cannabis nurseries in California, and the impact of new state policies on the cannabis nursery industry. Van is an awesome teacher, a great mentor, and easily one of the best professors I’ve had at Cal.
How did you get interested in woodworking?
I picked up woodworking in 2020 during the pandemic. I used to own an aquatic plant nursery business that required me to start building custom equipment like greenhouses, aquarium stands, and light stands.
It was a humble beginning: I learned from YouTube videos and by trial and error and primarily worked with a miter saw, drill, and some cheap two-by-four boards. I quickly became obsessed with the ability to manifest an idea with my hands but started to miss woodworking after moving to UC Berkeley at the start of my second year. After a little Googling, I found out that Jacobs Hall runs a makerspace with quality tools that is open to students at UC Berkeley.
I’ve been working out of there for the last two years, and have been able to teach myself fine woodworking and furniture making through more videos and trial and error.
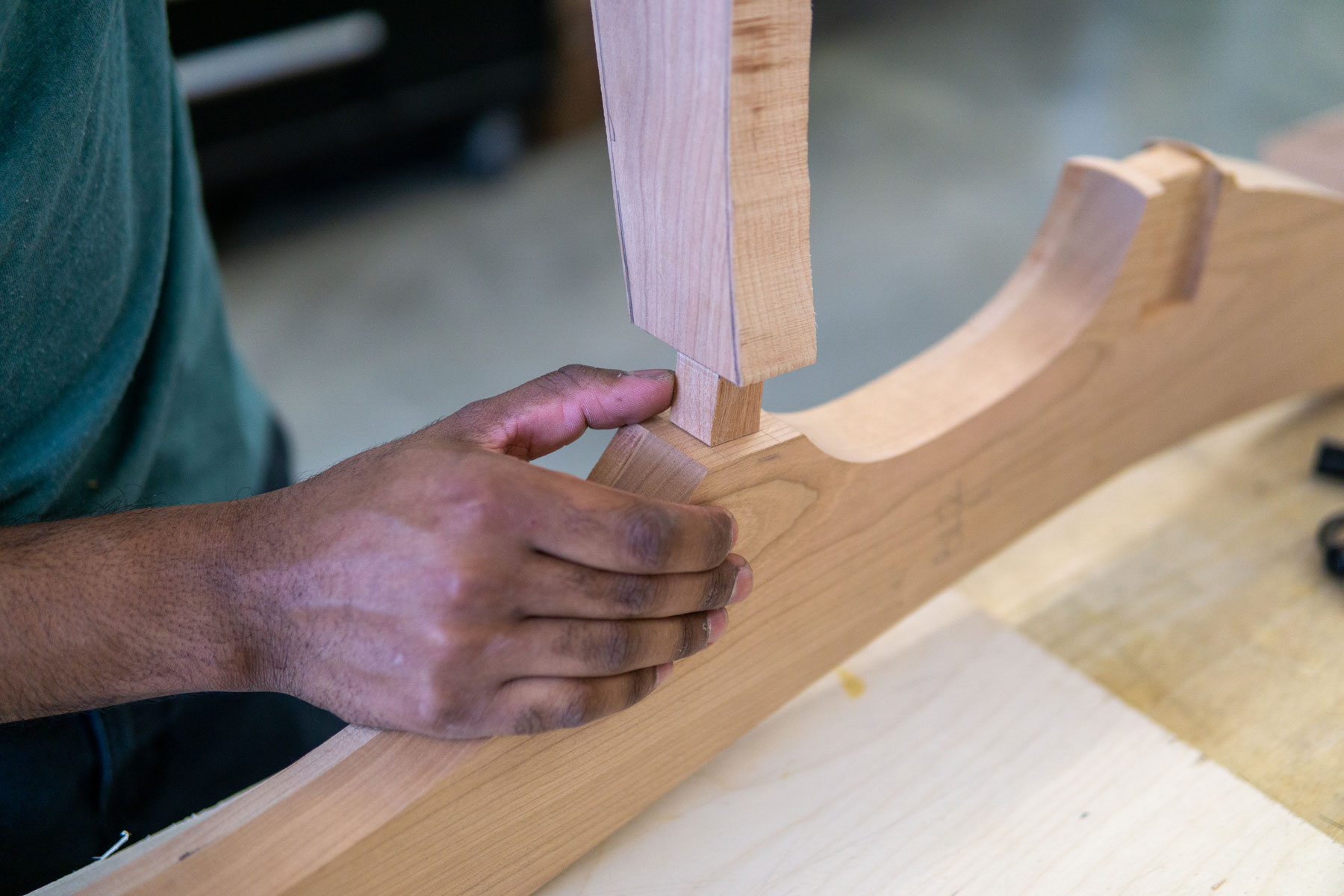
Photo by John Brechbill
What do you like to make most?
Furniture making appealed to me as a means of creating something beautiful, yet practical and long-lasting.
I usually start with an idea of what I want to build and the feelings that I want the piece to evoke. Wood furniture is a unique medium in that it engages multiple senses—sight, touch, and even smell—and my ideas for a piece will often center around how these senses are engaged or how that will translate to the feelings I want the user to have. After sitting on the idea for some time, I sketch the piece on paper before working on a 2-D model in Adobe Illustrator.
Using a laser cutter and the 2-D model, I create a scale model with the exact proportions and dimensions on the side, front, and top views. I go back and forth between the 2-D and scale models before I settle on the final dimensions. Once finalized, I take a few days to plan out my entire workflow—from milling rough lumber to applying the last coat of finish—before fabricating the final piece of furniture.
I consider all those processes to be part of the design phase, which is often the most difficult as it requires me to create a design that fulfills my original idea and goals while remaining strong and realistic to build with the tools I have available. Executing the design properly in the fabrication phase takes hand-skill, but it has been easier for me to master than the design and operations process. While the challenge and problem-solving in the design phase are among my favorites in the process, I truly enjoy the hand skills I develop and hone during fabrication.
Can you tell me more about the lounge chairs you built as a part of the Jacobs Design Showcase?
I chose to create these lounge chairs as my first statement piece and to push myself well beyond my comfort zone. Most furniture makers consider the chair to be the hardest piece of furniture to design and fabricate. It’s difficult to design because it must meet three simple criteria: it should be aesthetically pleasing, comfortable to sit on, and strong enough to bear the shifting weight of the human body over time. Constructing a chair, especially in the joinery, must be close to perfect because each joint bears an incredible amount of stress. Overall, the design phase took 50 hours, and it took me roughly 250 hours to construct the pair of chairs.
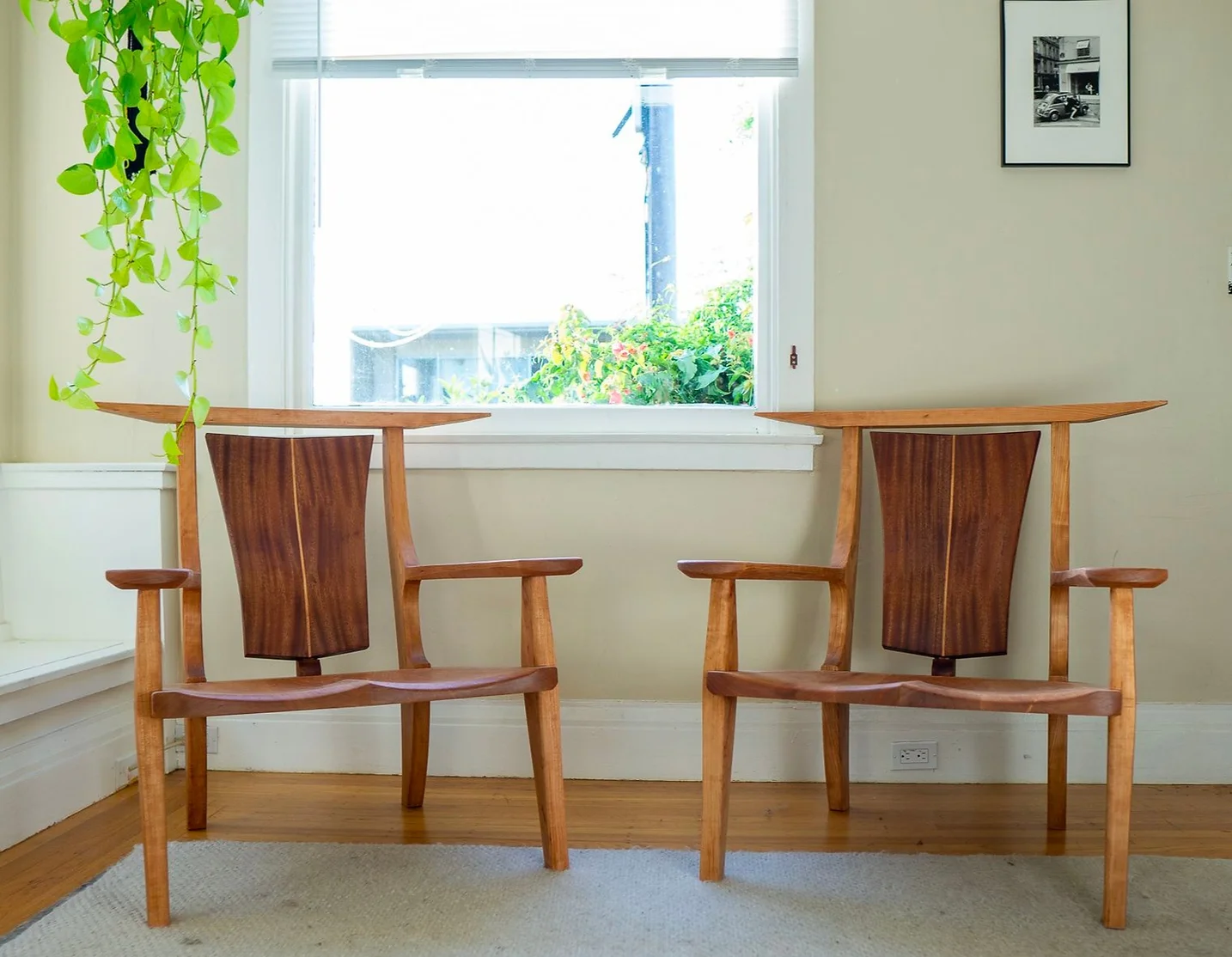
Photo by John Brechbill
My lounge chairs are made from American black cherry and ribbon sapele. Each features a deeply sculpted wooden seat, which is purposely wide in order to accommodate leg movement while seated and to give people enough space to spread out and lounge. A “floating” backrest sculpted in multiple planes provides optimal lumbar support, and it flexes slightly to accommodate the ever-shifting movement of the back while sitting.
As far as construction goes, all of the joinery was hand-cut with chisels and handplanes, and every component of the chair was sculpted by hand with spokeshaves and rasps. I’ve found that while hand tools are harder to master than power tools, they deliver more precise results. All of the joinery I cut by hand has been dialed in with a tolerance of less than five-thousandths of an inch. These chairs have been built with a level of quality that should last many generations
Do you know of a student or group in Rausser College involved in noteworthy research, community outreach, or extracurricular activities? Let us know by submitting a suggestion with this nomination form.